制震補強設計
導入事例
株式会社豊田自動織機 様
株式会社豊田自動織機
トヨタL&Fカンパニー
生産技術部
(右から)
主査 川嶋 伊久雄氏
課長 西谷 貴幸氏
旧耐震工場の制震補強に、
あえて”Is値”にこだわらず、
超高層建築の考え方を採用。
工期の半減を目指します。
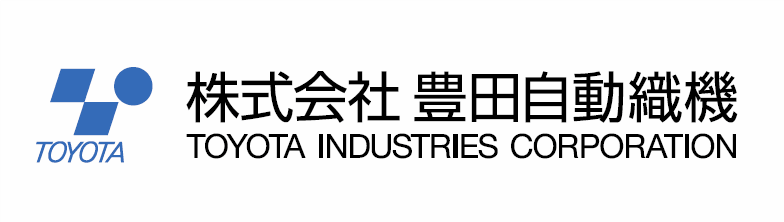
東日本大震災、熊本地震とここ数年大地震が続く中、いま切迫感を持って危険性が指摘されているのが南海トラフ地震(東海地震、東南海地震、南海地震)である。対象地域の企業は着々と対策に乗り出しているが、愛知県高浜市にある豊田自動織機高浜工場では、工場建屋で実施しようとしていた「耐震補強」を、構造計画研究所のシミュレーション結果を踏まえて「制震補強」に変更した。その決断の理由、もたらされるメリットなどについて、トヨタL&Fカンパニー生産技術部 主査 川嶋伊久雄氏、課長 西谷貴幸氏にうかがった。
目次
「Is値0.6以上」にすればそれで本当にいいのか?
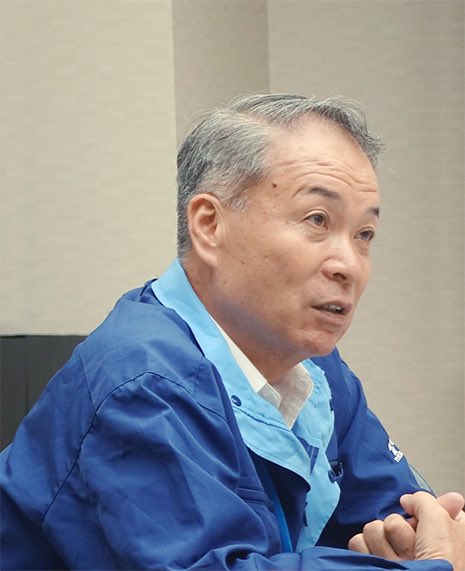
生産技術部 主査 川嶋伊久雄氏
まず、工場の概要から教えてください。
当社は、フォークリフト、カーエアコン用コンプレッサーなどの世界トップメーカーです。国内に10の拠点があり、高浜はフォークリフト生産工場です。敷地内は建屋が多数あり、今回補強の対象になったのは、旧耐震の工場数棟および実験棟です。
その中でいち早く検討を進めたのは、建屋Aでした。当社の震災対策は、対象とする建屋の優先順位などを事業部ごとに決め、実行に移します。建屋Aを最優先にしたのは、建屋面積が最大であることと中で働く従業員が多くいて、「人口密度」が最も高いことが理由です。
当初は、ゼネコンが提案する「耐震補強」で検討を進められたとか。
ご存じのように、耐震改修促進法などには、「Is値(※1)0.6以上」という耐震指標が記載されており、それを満たさない建物は「耐震補強の必要性あり」と判断されるんですね。つまり、国は「Is値0.6以上となるように耐震補強をせよ」と言っているのです。
ですから、当工場でもそれに沿った検討を開始したわけですが、経営陣からは「0.6と0.55は実際どれほど違うのか?」といった詳細な質問も結構ありました。ところが、誰もそれに対して明確に答えられませんでした。逆に対策を依頼したゼネコンに「Is値0.6をクリアすれば、大地震に耐えられるんですよね?」と聞いても、そこは技術者同士、はっきり「イエス」と言わないわけです。
そんな頼りなさも覚える状況で、該当棟に対するゼネコンの耐震補強案が出てきたのは、2014年の夏頃でした。ところがそれは、工期もコストも「大いに問題あり」のプランだったのです。
建屋Aだけで15年、すべて完了するのに18年かかるというものでした。
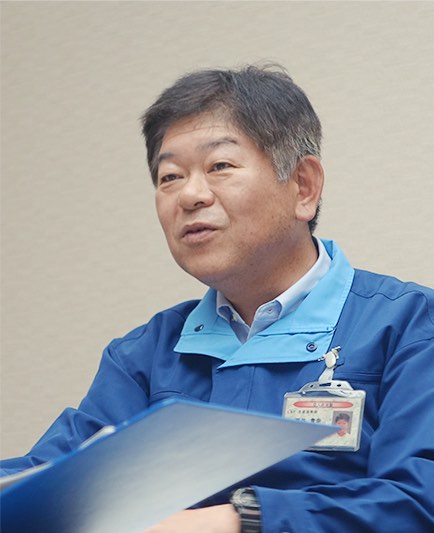
生産技術部 課長 西谷 貴幸氏
当初提案された工期では対応が間に合わないと判断されたわけですね。
これでは、「明日来るかもしれない」という巨大地震への備えとしては非現実的でしょう。当然のごとく、経営陣からは「もっと工期もコストも削減できる方策は考えられないのか」と。
そこで白羽の矢を立てたのが、構造計画研究所(以下、KKE)でした。建築構造や地震対策に強く、以前当社の別の工場の耐震補強に関するシミュレーションを依頼したことがある、という話を聞いたことがありました。今回も、シミュレーションを基に、工場を実際に揺れから守るリーズナブルな補強に向けた知恵をいただきたいと考えたのです。
あえて付け加えれば、経営陣からは「どうしてKKEなのか、客観的に評価できる材料を」というリクエストもありました。シミュレーション自体、決して安い「商品」ではありませんでした。我々が経営陣に提出したのは、実際の建物を使ったコンペでKKEが優秀な成績を収めていた、という事実です(※2)。地震波で想定される衝撃のシミュレーションを、実際に建物を揺らして検証するというもので、論より証拠の説得力がありました。
※1 Is値(Seismic Index of Structure:構造耐震指標)
Is値とは地震力に対する建物の強度、靱性(じんせい:変形能力、粘り強さ)、経年劣化等を考慮して算出される数値で、耐震性能の基準値として用いられている。「建築物の耐震改修の促進に関する法律(耐震改修促進法)」の告示(平成18年度国土交通省告示 第184号と185号)により、震度6~7程度の規模の地震に対するIs値の評価については、Is値が0.6以上であると「倒壊、または崩壊する危険性が低い」と定められている。
(一般財団法人 日本耐震診断協会WEBサイトより引用。
http://www.taishin-jsda.jp/is.html)
※2 ブラインド解析コンテスト
KKEは2009年に独立行政法人防災科学技術研究所が実施した、E-ディフェンス震動台による鉄骨造建物実験を対象としたブラインド解析コンテストにて、4部門中2部門において最優秀チームに選ばれた。
ニュースリリース:
https://www.kke.co.jp/news/pdf/2009/NewsRelease_e_defense.pdf
公式サイト:
http://www.bosai.go.jp/hyogo/blind-analysis/2008/index.html
操業を止めずにスピーディな対策が実行できる「制震」
“As-Is”すなわち「現状のまま何もやらない」場合と、ゼネコン提案による耐震補強をやった場合、想定される大地震に襲われたら建屋Aがどうなるのか、KKEに解析してもらいました。そうしたら、As-Isは当然壊れる、そして、「耐震」をやるともっと早く壊れる、と。
耐震補強をした方が早く壊れる、というシミュレーションの結果は衝撃的ですね。
工場のある地盤は、大規模な液状化が起こる可能性はほとんどないのですが、やや柔らかいと聞いています。その状況で何がなんでもIs値 0.6以上を確保するために、と建屋の高いところにも補強材を入れたりすると、揺れ方によっては、それが逆効果になってしまうことがわかったわけです。ちなみに、以前、KKEにシミュレーションしてもらった別の工場は丘の上のしっかりした地盤に建っており、耐震補強で共振現象は発生せずにOKという診断でした。
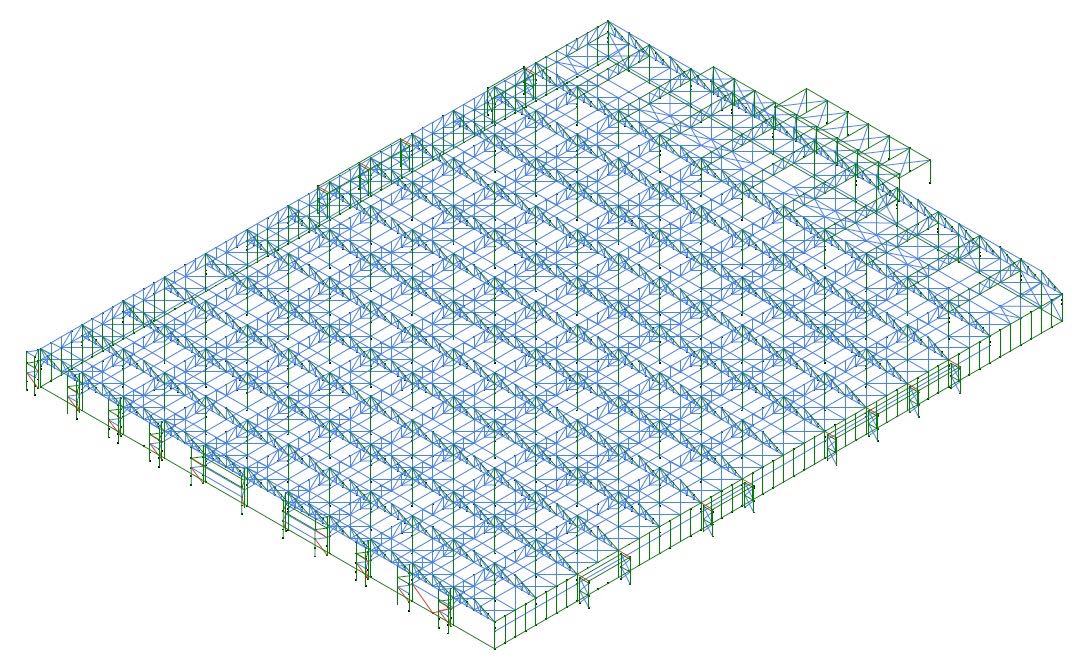
▲ 建屋A立体解析モデルのパース図
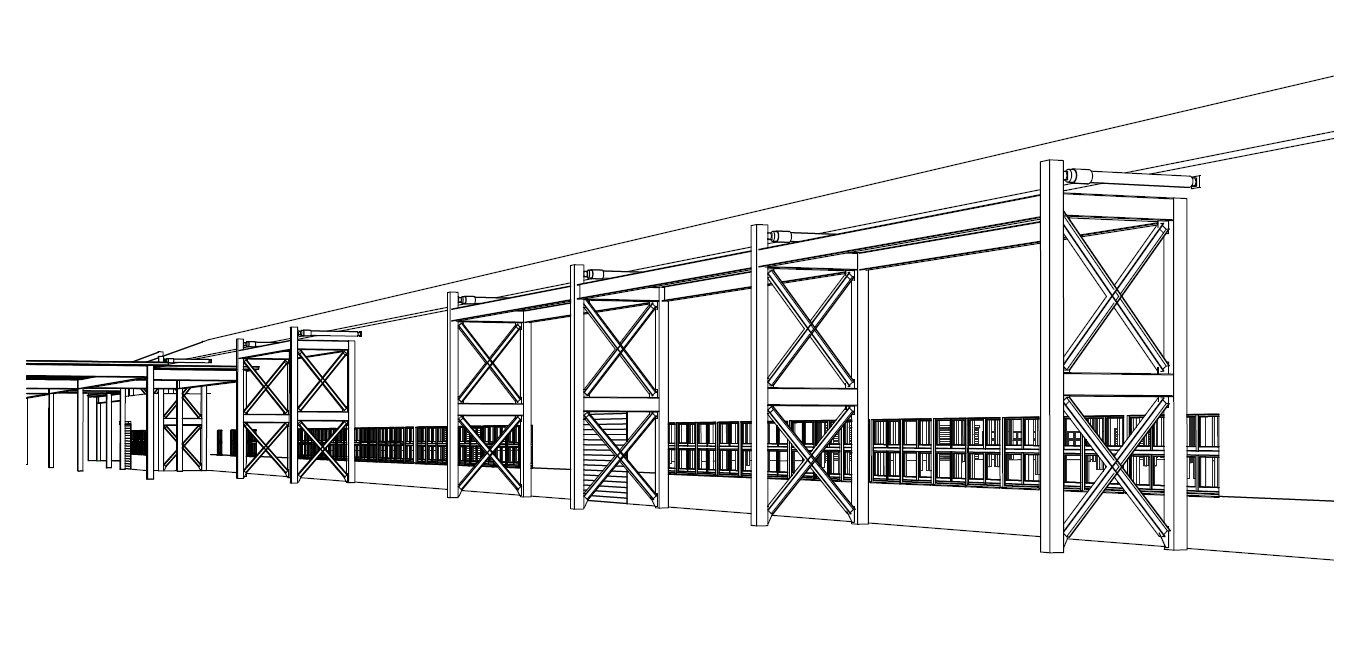
▲ 制震ダンパーの模式図
いずれにせよ、この結果を受けて、2014年末には建屋Aの耐震補強はNG、というのが正式に決まりました。決まったことはともかく、新しい対策を具体化しなければなりません。そこで、KKEに引き続き調査、検討を依頼したのです。
「お客様にとっての安全・安心」という観点から検討の末、KKEが提案したのは「耐震」ではなく「制震」でした。建屋そのものを強化するのではなく、建屋の外に多数のダンパーを設置して、地震の揺れを吸収してしまおう、という方法です。
その「建屋の外に設置」というのが大変重要なんですね。いくら地震対策が重要だからといって、その間工場の操業を止めるわけにはいきません。ランニングさせながら対策を実行する必要があるわけで、実は以前の耐震補強の工期やコストの問題は、そのことが主な原因になっていました。
とはいえ、逆に「工期やコストを縮減できればいい」というものでも、もちろんありません。当社も各工場毎にBCP(事業継続計画)を設定しており、地震リスクについては想定震度等を決めています。今回の制震補強は、そのリスクに耐える事のできる性能目標になっています。
当社の担当者も含め、多くの議論、検討を実施されたと聞いています。
KKEは、常にベストのソリューションを提供してくださいますので、こちらはそれが実現可能なのかを一つひとつ詰めていったという感じです。例えば、今回のプロジェクトには、最初から本社の施設管理の担当者にも入ってもらいました。ダンパーを外付けするやり方のメリットはさきほど申し上げましたが、実は工場の周囲にはユーティリティ設備などの「障害物」もあります。できるだけそれらを移動させて、ダンパーを設置できる環境にするためです。
こういう話はゼネコンに全委託なら、工期と費用をすり合わせて「あとは責任をもってやってください」で済むかもしれませんが、今回は違います。我々としても前例のないプロジェクトでしたから、「耐震」ではなく「制震」だという事前検討からスタートさせて、制震補強の基本検討、さらに詳細設計、施工と細かくステップを踏んで進めたわけです。
オーダーメイドで対応するのが「地震対策」のセオリー
建屋Aの工事は、すでに始まっているわけですね。
KKEとともに制震補強の詳細な検討を進め、2015年末には採用を正式決定し、2016年の年初から補強工事に着工しています。当初の耐震補強案に比べて工期は検討期間も含め半減の目処がつき、コストも前のやり方の半分程度にまで削減することができました。
補足ですが、全棟のうち数棟をKKEにお願いし、他の棟については建屋自体の建設に携わったゼネコンに依頼しています。ただし、ゼネコンに依頼している分の棟も含め補強のコンセプトは、どの棟も基本的に変わりません。
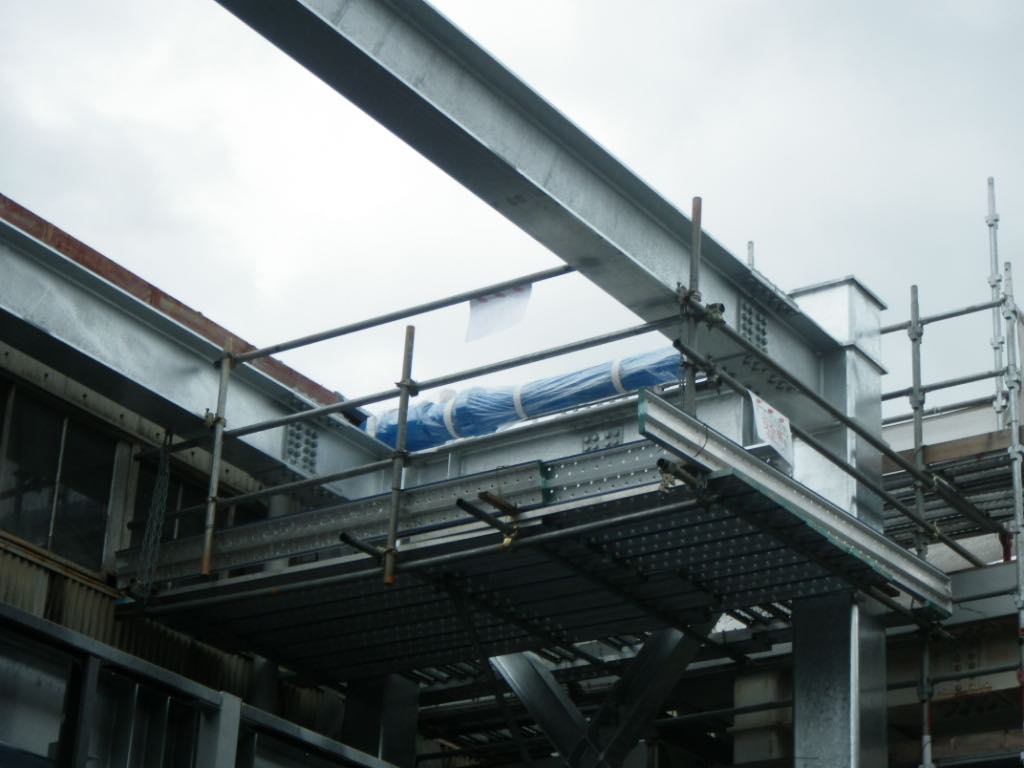
▲建屋外部での制震補強工事の様子。建屋内部では操業が続けられていた。
地震対策は原則、事業所ごとに計画するというお話でしたが、今回の制震補強が他工場で採用される可能性はありますか?
それはあると思います。ただし、工場ごとの立地環境がありますから、今回のやり方がすべてに導入できるかというと、そうはいきません。例えば、外付けのダンパーは、建屋から4~5mほど突き出る形になりますから、周囲にそれだけのスペースのあるのが条件です。さきほども言ったように、地盤の条件がよければ耐震補強が有効だと思います。
我々の発想としては、まず大地震で建屋がどうなるか、どんな対策が有効なのかを知る道具としてシミュレーションを使います。そのうえで、今回のようにダンパーを使った制震補強が適していればそれを使いますし、耐震のほうがベターという結論が出ればそうします。状況によっては、両者のハイブリッドだってありうるでしょう。
重要なのは「そこで最適な対策は何なのか?」ということではないでしょうか。補強は、まさにオーダーメイドだと思うのです。そうした検討なしに「Is値0.6以上を実現しているから大丈夫」という考え方は、少々、本末転倒な気がします。
専門家に相談し地震対策として問題なし
今回はIs値ではなく、その工場に最適な制震補強になりました。
そうですね。Is値0.6以上の耐震補強をした場合、仮に地震で崩れても「基準に則った補強を行いました」と言えますが、私たちが目指すのはあくまでも地震で壊れない対策です。
そこで考えたのが、超高層建築で実施されている第三者による「耐震診断評定」です。ただ、超高層ビルに対して行うのと同様の評定を築40年の工場の制震補強に際して実施するというのは、さすがに時間もコストもかかりすぎますので、専門家に相談することにしました。具体的には、建築物の構造安全性、耐震安全性が専門の名古屋工業大学 井戸田秀樹教授(※3)にお願いし、我々の基準や、制震補強の考え方を説明し、それに対して押さえるべき事項をご教示いただきながら、対策を練り上げてきました。
その結果、建屋Aに関しては、地震対策として問題ないと判断いただいたんですよね。
はい、その通りです。万が一、地震の際に我々の想定していなかった被害が生じた場合、「専門家の確認も得て、こうした考え方で対策をしました」ときちんと説明はできます。他の棟に関しても、同様の基準および補強の考え方で対策を検討しています。
※3 本事例に関する制震補強の考え方は専門的にもまだ珍しい取り組みのため、2016年8月の日本建築学会大会で発表されました。
「梁川幸盛(構造計画研究所)・新美仁(豊田自動織機)・井戸田秀樹(名古屋工業大学)「粘性ダンパーによる鉄骨造大型工場の制震補強検討」日本建築学会大会梗概集2016年8月, No.22442, pp.883-884, 2016年8月.」”
KKEの提案から、多くのことを学ぶことができた
あらためて、当社のここまでの仕事については、どのように評価なさっていますか?
本当に、親身になってやっていただきました。新たな提案に驚いて、社内が揉めたりするくらい、考え抜いてもらいました。
それは、どんな提案だったのでしょう?
すべて外付けのダンパーでいく、とみんなが信じていたわけです。しかし、結果的に1カ所だけ、壁の中に入れる面内ダンパーになったのです。調べてみたら、そこには地下タンクがあって、どうしてもその上には設置できませんでした。
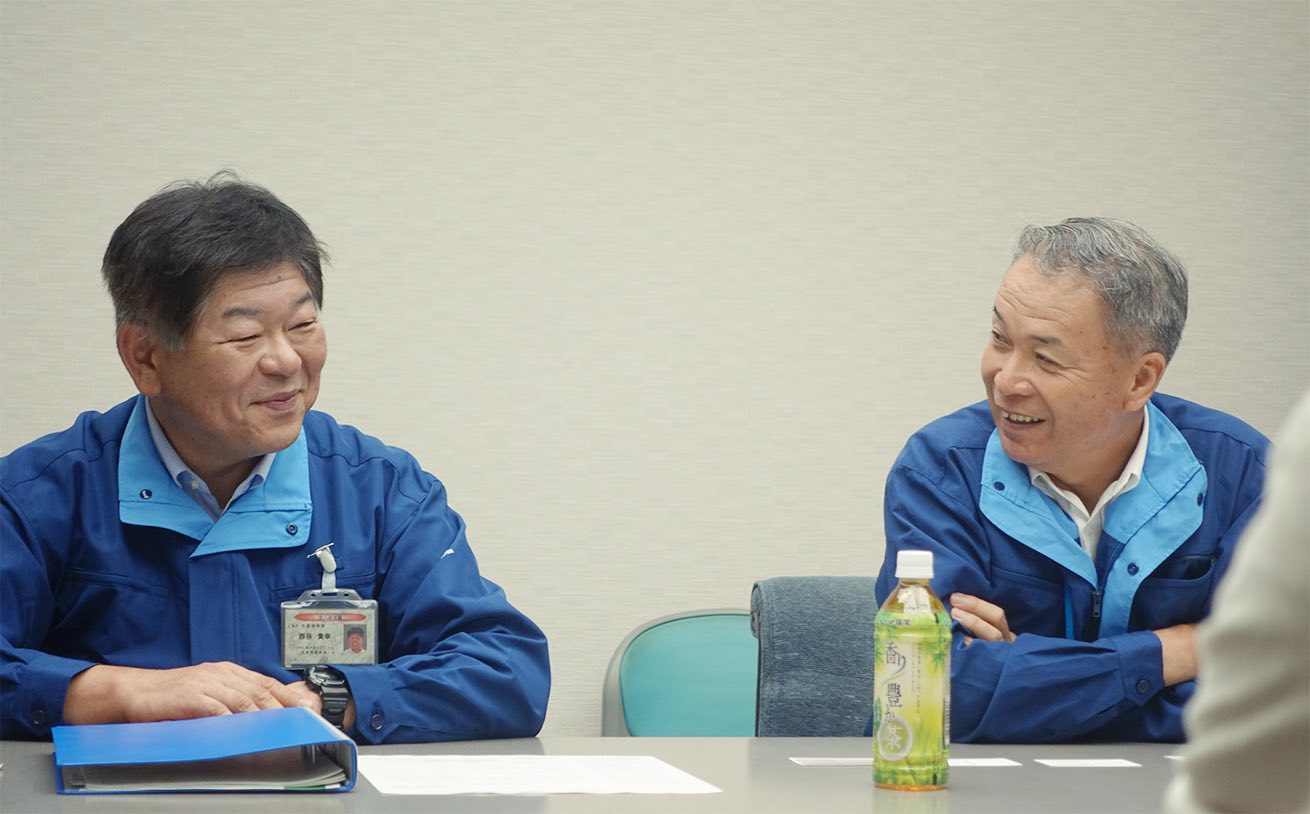
ところが、そう決めたら新たな発見もあって、そのように面内ダンパーにするほうが、外付けの方式よりも工期もコストも有利だということがわかりました。ただし、これもどこにでも入れられるという話ではなくて、工場内で生産設備の干渉がない壁面に限られます。なので、次の工場からは、壁に細工のできる箇所については面内ダンパー方式にすることを基本に、設計を進めています。
本当にオーダーメイドだったんですね。
「ステップを区切って検討を進めた」という話をしましたが、そういう建屋Aのプロジェクトを通じて、KKEから我々も多くのことを学びました。おかげで、次の建屋Bの制震補強に向けては、こちらから提案できるくらいの知識を持つことができました。
当社に対して、今後の期待や要望などがございましたら教えてください。
すべてのプロジェクトが終わるまで、フォローをお願いしたいということに尽きます。個人的には、御社のミッションに「エンジニアリングで新たな付加価値を創る」とうたっているのを聞いて、非常にいい会社だと感銘を受けました。当社のようなメーカーもまさにそうで、世界と戦う武器は技術力以外にないわけです。今後もその志を胸に、各方面で活躍、貢献されることを期待しています。
取材日:2016年7月
株式会社豊田自動織機について
設立:1926年11月18日
本社所在地:愛知県刈谷市豊田町
ホームページ:
https://www.toyota-shokki.co.jp/
※記載されている会社名、製品名などの固有名詞は、各社の商標又は登録商標です。